Field Repairs
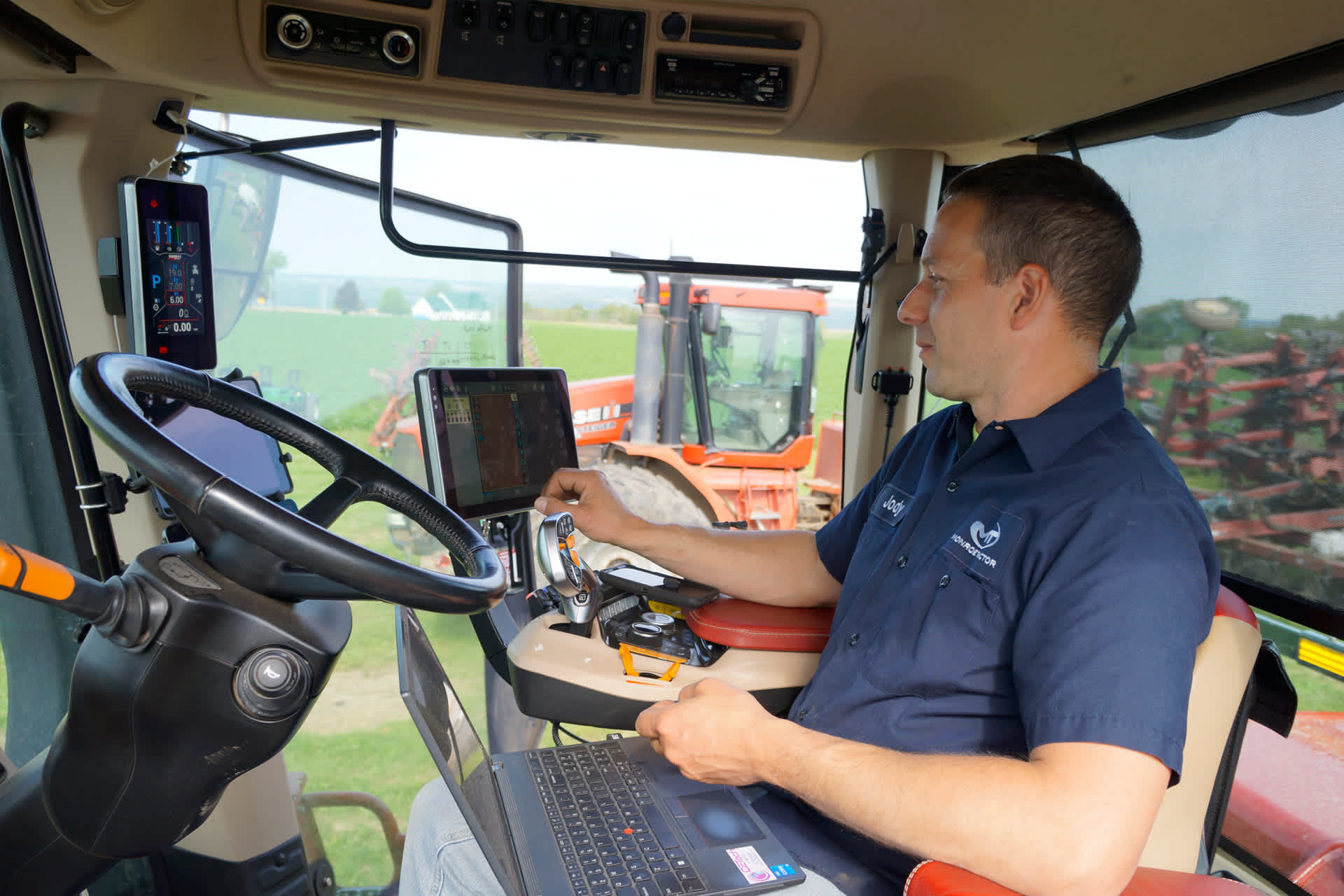
There are nearly 2 million farms and ranches in the United States. Every day, farmers and ranchers across the country spend hours sowing seeds and tending to crops and livestock. So it’s crucial that their high-tech machinery is in perfect working order. Yet tractors, combines, and other pieces of farm equipment break down all the time. When they do, agricultural technicians head out to get them up and running.
In this line of work, a can-do attitude is a big plus. It’s what Nick Helton and Jody Fisher take with them on service calls. Helton is a service technician for American Implement, a John Deere parts and equipment dealer with locations all over Kansas. Fisher is a technician for Monroe Tractor, in North Java, New York. Both men start work as early as 6:00 in the morning, wherever equipment needs fixing.Â
Your Hot Job spoke with them about how they got started, what the job is like, and how it’s rapidly changing.
“I’ve always been deeply rooted in agriculture.” —Nick Helton
Growing up, Helton was involved with 4-H and Future Farmers of America. His first job was working for a farmer. In college, Helton took agricultural classes and focused on an animal science degree. After a few years in the automotive industry, he got a chance to become an agricultural service technician.Â
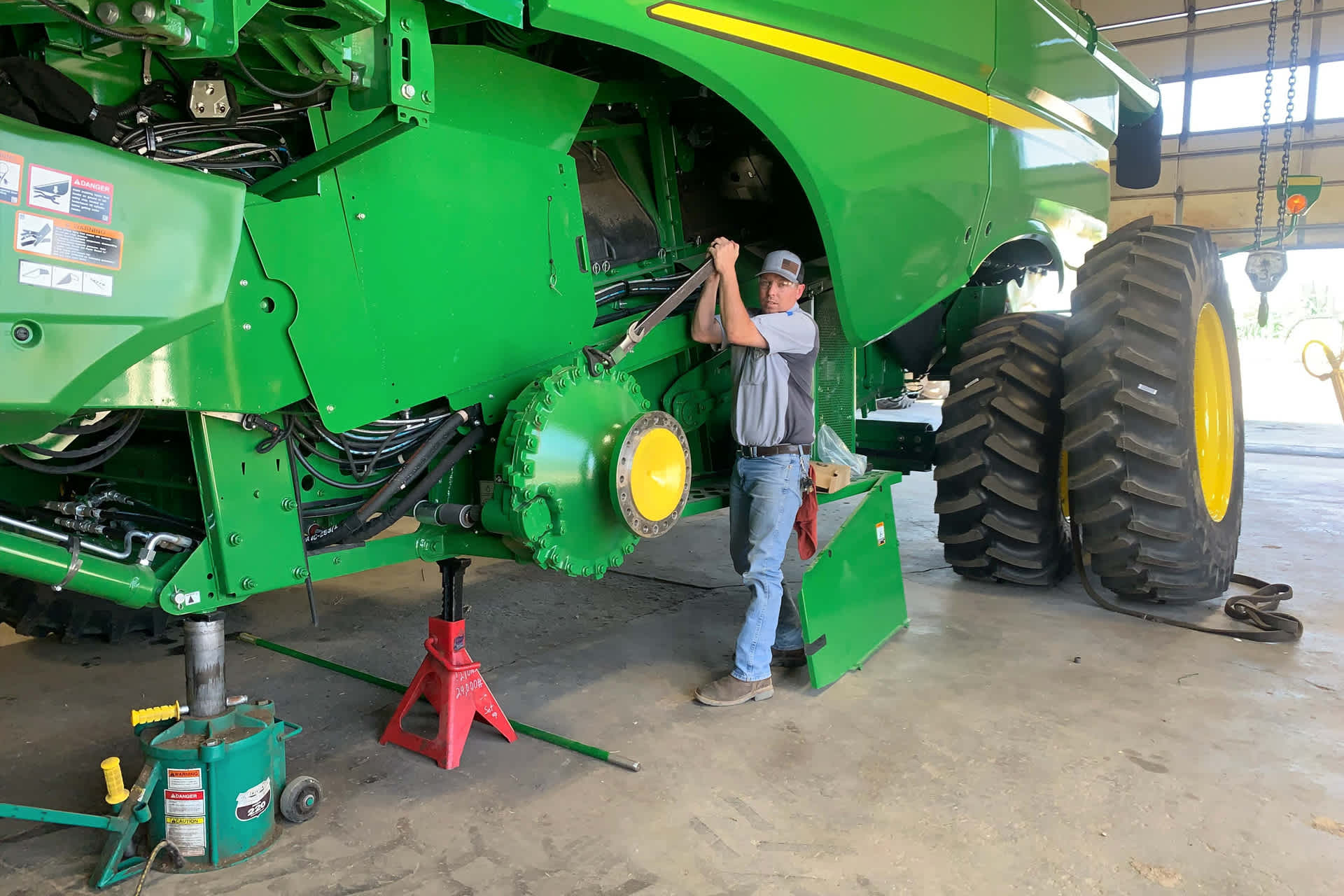
Like Helton, Jody Fisher was also involved in agriculture from an early age. He played with toy tractors as a child, and started working on the real thing when he was 14. In college, he focused on what came naturally: agricultural mechanics.Â
“To me, it’s like being a doctor. It’s rewarding when you figure out the issue and can get the customer moving.” —Jody Fisher
Just knowing what you’re up against is half the battle, Fisher says. A lot of his calls have to do with electrical issues. Sometimes, he can make a diagnosis in minutes. Or he can spend hours scanning schematics to track down one broken wire.Â
There are also times when a technician has to completely dismantle a piece of equipment. “What’s most rewarding,” Helton says, “is when it works after the reassembly.”Â
“It could be snowing and below zero, or 108° with a brisk 40-mile-per-hour wind.” —Nick Helton
Working in all kinds of weather is one of the many challenges of being a service technician. Another is constantly thinking about replacement parts. When possible, Helton gets the parts he needs to complete a job before heading out into the field. But often the right parts are not in stock. That’s where expertise and ingenuity come into play. Helton enjoys the challenge of fabricating parts on the fly. A quick fix lets a farmer get back to work until the replacement part becomes available.Â
“The most important tool I have is my laptop.” —Jody Fisher
Fisher’s truck is loaded with electric drills, screwdrivers, wrenches, and other tools needed for hands-on fixes. For issues that are more complex, he uses his computer to access fault codes and other programs needed to repair modern machinery. Fisher says technology has changed the way technicians work.Â
Helton agrees. “When I first started out . . . we were still using paper diagnostic charts and repair manuals,” he says. Today, he might use his laptop to fill out paperwork, access a digital manual, or upload software onto farm equipment. He also uses it to complete a minimum of 25 credit hours of training a year. “Equipment today is to the point it can drive itself,” Helton says. “So extensive training is needed.”